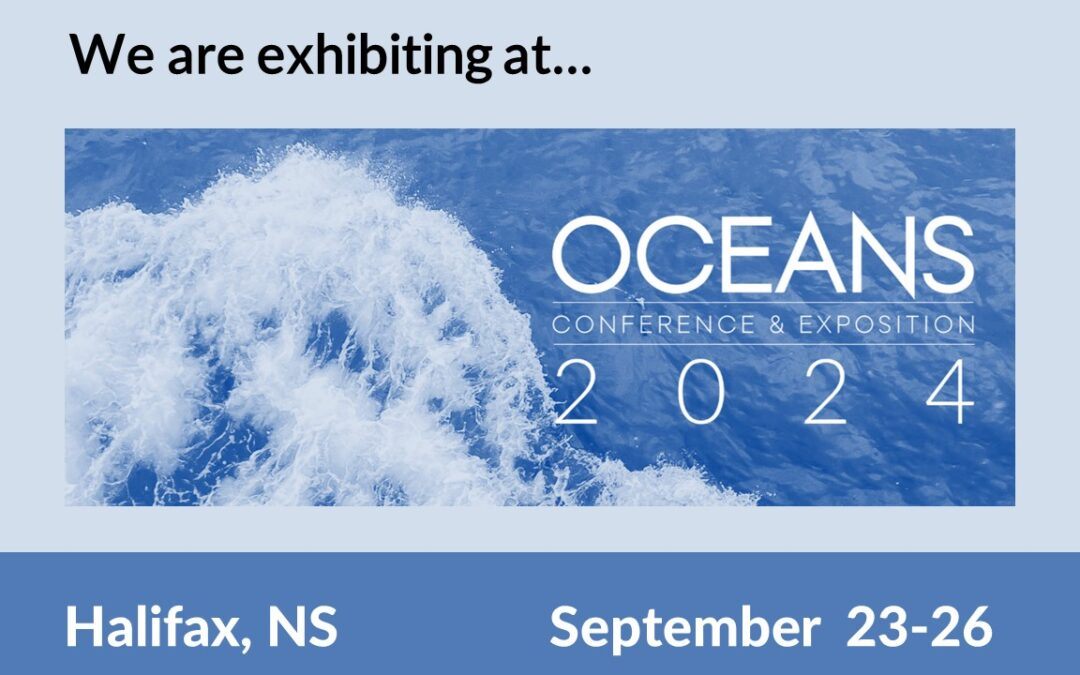
Exhibiting at Oceans 2024
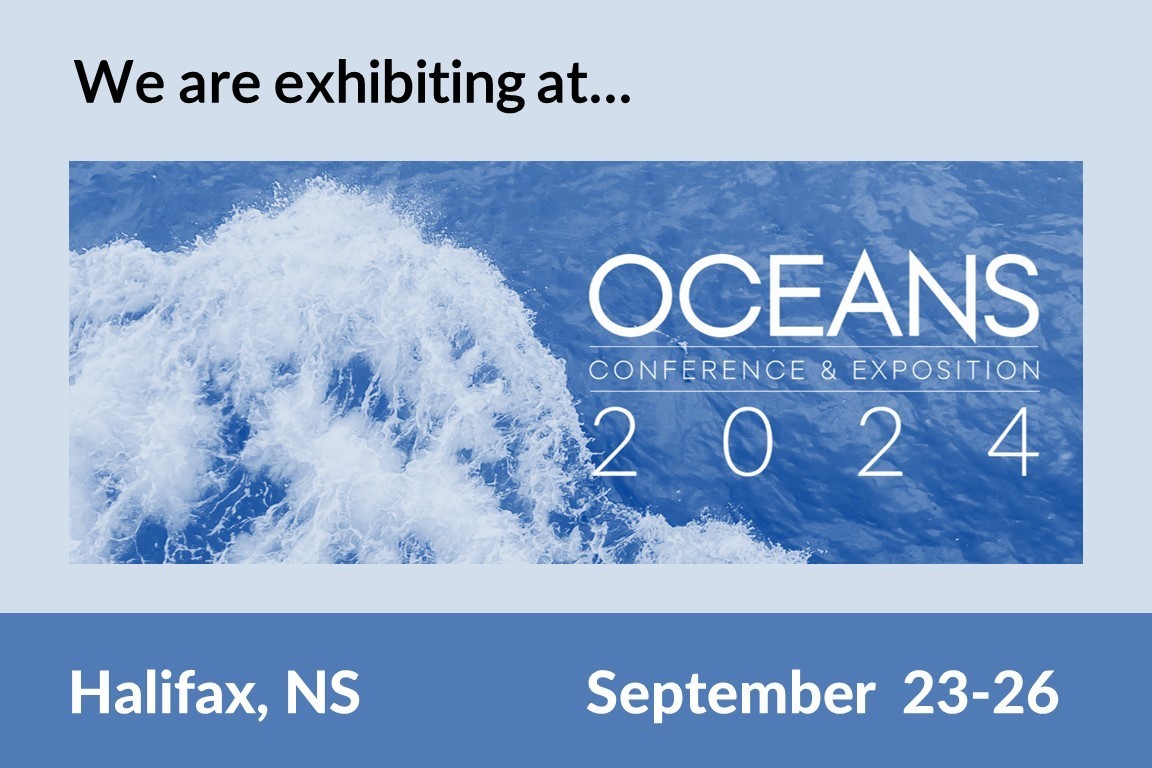
Exhibiting
DeepWater Buoyancy will be exhibiting at the 2024 Oceans Conference and Exposition. The event will take place September 23-26, 2024 at the Halifax Convention Centre in Halifax, Nova Scotia.
Please visit Dan Cote (Sales Manager) and Jordan Tremblay (Sales Engineer) at Booth 304.
About the Event
OCEANS is an annual event for global marine technologists, engineers, students, government officials, lawyers, and advocates. At OCEANS 2024 Halifax, industry thought leaders gather for four days to highlight relevant topics and current trends while creating a community of learners and influencers who consistently advance research, practices, and policies for the marine field.
Learn more about the event HERE
Send us an email to schedule a visit at the show with DeepWater Buoyancy’s Sales Manager, Dan Cote. dcote@deepwb.com
Why We Attend
DeepWater Buoyancy is the world’s largest supplier of subsea buoyancy to the ocean science community and provides products to all offshore, subsea markets. The product line is now over 40 years old and is known throughout the world. It provides critical product design and development for even the smallest clients, sometimes producing only one custom solution. This allows all ocean engineers, project managers and scientists to get the subsea buoyancy product that is fit for their project.
Much of the work that is done in the challenging environment of deep water requires syntactic foam buoyancy. When it comes to syntactic foam, DeepWater Buoyancy is a critical partner to the offshore subsea market. Exhibiting at the Oceans conference will allow us to visit in person with end users, ocean engineers, and partner companies. It will also allow us to spend time with our international sales representatives like DASCO Equipment of Canada.
See our full product offering HERE.
About DeepWater Buoyancy, Inc.
DeepWater Buoyancy creates subsea buoyancy products for leading companies in the oceanographic, seismic, survey, military and offshore oil & gas markets. Customers have relied on our products for over forty-five years, from the ocean surface to depths exceeding six thousand meters.
Learn more at www.DeepWaterBuoyancy.com