Aug 23, 2017
Introduction
DeepWater Buoyancy, Inc. has added a new product to their successful line of Mooring Line Cable Fairings. The new fairing is designed to accommodate 1/4″ jacketed wire rope. It is the latest item in the company’s portfolio of products for subsea mooring systems.
Vortex-induced Vibration
Under certain flow conditions, taut mooring lines can vibrate or “strum”. The strumming is caused by vortices that result from the water passing over the line diameter. Strumming not only creates cable fatigue, it can have a detrimental effect on instruments in the mooring string.
Mooring Line Cable Fairing
DeepWater Buoyancy’s mooring line cable fairings reduce strumming by eliminating this vortex action. Less strumming means less fatigue on the line. Additionally, the fairing design reduces drag on the mooring line resulting in less mooring layover. As an example, the drag coefficient for a 3/8” jacketed wire cable is 1.20, whereas the mooring line fairing is 0.17. This is an improvement of over 85%.
Fairings are made of durable ABS plastic. They are easily loaded onto the mooring line during deployment simply by separating the ends of the fins and installing over the line.
Unlike other solutions, this product can be installed over select portions of the line, requires no maintenance, does not suffer from tangling problems, and resists biofouling.
The standard units are designed for 1/4″ and 3/8″ jacketed wire rope and are 12” in length. Other diameters and lengths can be produced upon request. End clamps are also available to limit the vertical movement of the fairing on the line.
Learn More
Learn more about mooring line cable fairings HERE
Download a datasheet HERE
See all our product types HERE
About DeepWater Buoyancy, Inc.
DeepWater Buoyancy creates subsea buoyancy products for leading companies in the oceanographic, seismic, survey, military and offshore oil & gas markets. Customers have relied on our products for over thirty-five years, from the ocean surface to depths exceeding six thousand meters.
For further sales information: Dan Cote, Sales Manager | sales@deepwb.com | +1 207 502 1400
For further company information: David A. Capotosto | davidcap@deepwb.com | +1 207 468 8545
Feb 3, 2017
For the next installment in our series of technical articles, Rob Morris, Product Line Sales Engineer for EdgeTech, examines how to choose the proper acoustic release for an application.
Introduction
In my role as Product Line Sales Engineer for acoustic releases and actuated products, I am frequently asked, “What acoustic release should I use for my application?”
The choice of release depends on many factors, such as water depth, length of the deployment, release load and lift load, and expected ambient noise. Biofouling or silting can also be a problem in some areas and should be taken into consideration as well. Following are some examples of applications and the related solutions.
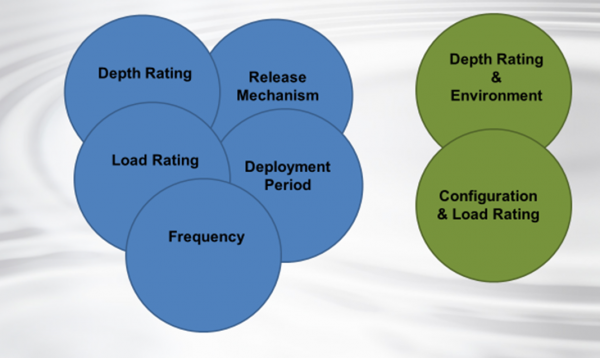
Factors affecting the selection of an acoustic release.
Deploy an in-line mooring with multiple instruments in deepwater (5000 to 6000 meters) for 1 to 2 years
In this case, I would recommend a deepwater acoustic release with full transponding capability that can handle a large anchor (1000kg or more). Because of the cost of the mooring instruments and the value of the data, it is critical the mooring be recovered. Therefore, a tandem release set-up for redundancy would also be desirable.
The transponding capability (tilt, release status and ranging) is very useful for deepwater operations to locate the mooring before releasing, to receive release status, and to track the mooring as it rises to the surface. Please also consider that depending on depth and how much buoyancy and drag the mooring has, it could take up to an hour for the equipment to reach the surface. (See Jon Wood’s article on buoy ascent here. LINK) And if there are subsea currents in the area the mooring could be a couple of miles away when it finally reaches the surface.
Shallow water and a heavy load
Sometimes scientists and ocean researchers find themselves in need of deploying a heavy package in shallow to mid-water settings and there is a desire to use an existing acoustic release that was acquired previously based on water depth requirements, but not release loads. To address the situation a strongback can be added to the acoustic release as a cost-effective way to increase the release and lift load rating of a mid-water acoustic release.
Deploy an in-line mooring in shallow water in harsh environments, such as the High Arctic, for 1 year
Because of the remote location and the harsh coastal environment, the PORT MFE (Push Off Release Transponder) is ideal for deployments of this kind. The mechanical drive off system is the best choice for deployments where normal release mechanisms can experience growth or sediment build up. Unlike traditional releases that use a metallic lever mechanism for their release function, the PORT uses a non-corrosive link that is physically pushed off of the unit when commanded. This eliminates the often troublesome issues of biofouling and corrosion that causes failures in other units.
Here is a real life example of this. 20 moorings were deployed to log fish tracking information in a remote area in the High Arctic. The user planned to recover the moorings in 12 months, but due to weather conditions and the inability to schedule ship time, the moorings were left in place for 4 years. When the user finally made it back to the deployment site, they were very happy to recover all 20 of the releases. The Push Off Release mechanism easily overcame the heavy marine growth that had built up over 4 years.
The releases were covered with so much marine growth they can barely be seen in the photo below.
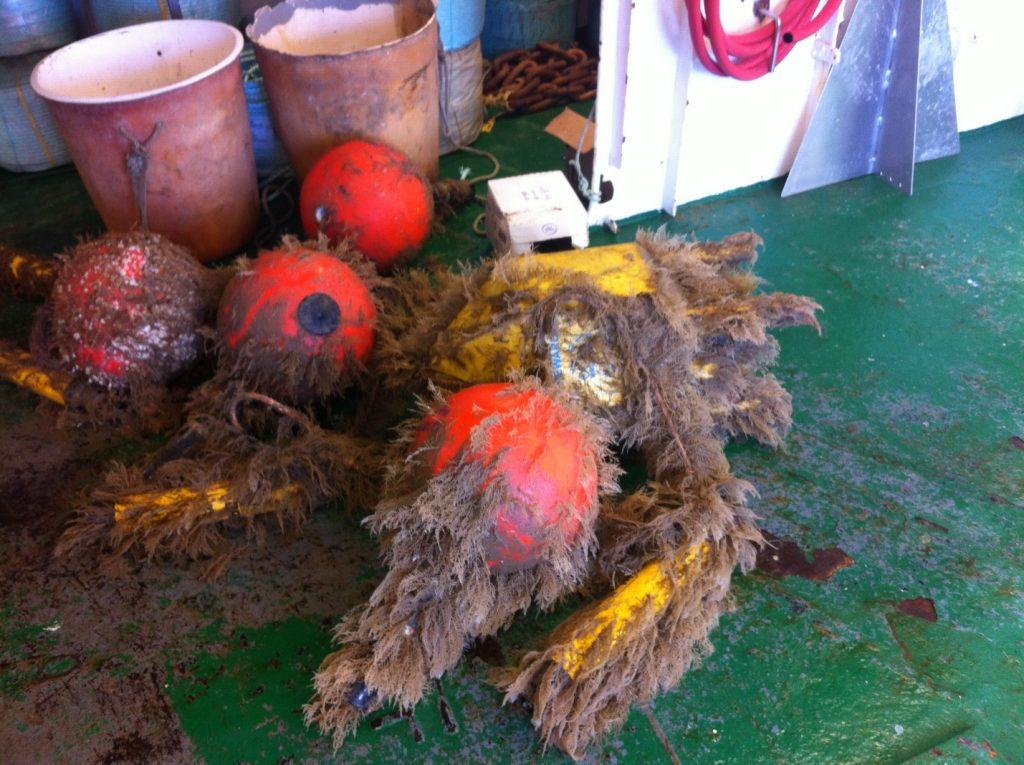
Marine growth covering buoys deployed in shallow water.
Deploy and recover an instrument package including the anchor leaving nothing behind on the seafloor
Sometimes there are regulations that require all equipment to be removed from the seafloor when the job is completed. Sometimes the solution for this application would be to use a Pop-up system. A Pop-up system combines the acoustic release, flotation and line in one package. When acoustically commanded by a deck unit, the acoustic release and the top portion of the pop-up package will float to the surface. The release and surface flotation remains connected to the bottom section by a high strength synthetic line for easy retrieval leaving nothing behind on the seafloor.
Deploy and recover an instrument package in an area where fishing trawlers work
Often science and commerce work in the same space. So in the case where instruments need to sit on a seafloor where trawling is done, the solution is a TRBM (Trawl-Resistant Bottom Mount) with integrated flotation and an acoustic release.
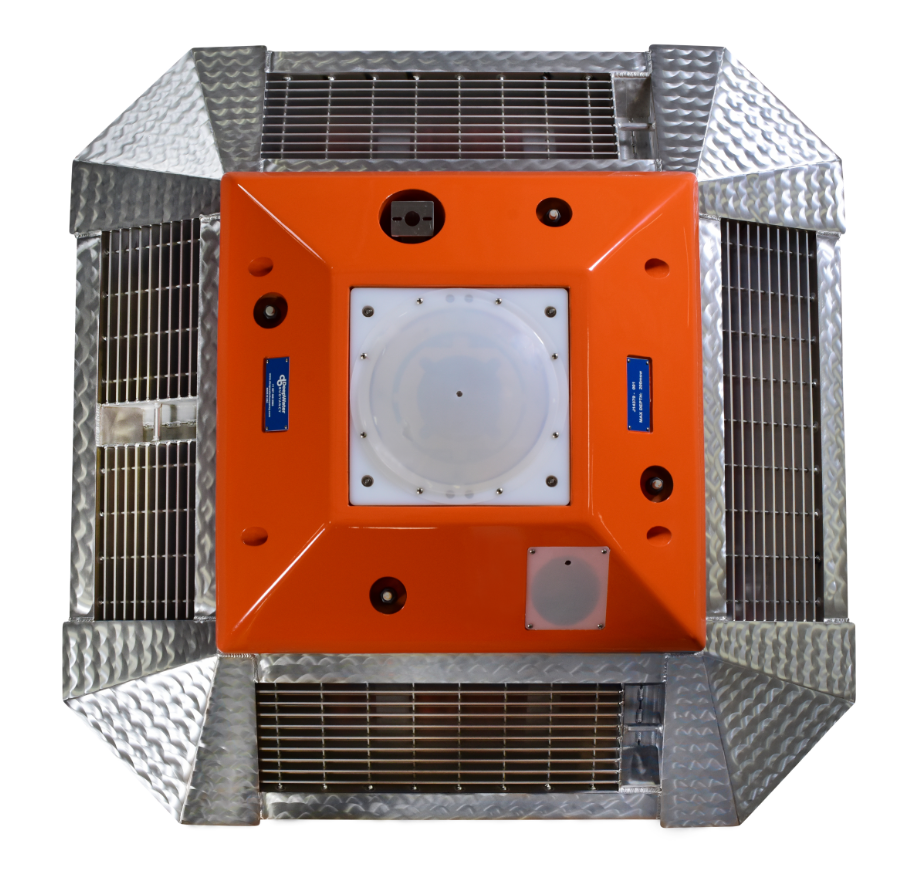
DeepWater Buoyancy Trawl-Resistant Bottom Mount
In this design, all the instruments and an acoustic release are integrated into a low-profile, trawl-resistant, deployment package. When commanded, the release activates and the flotation module will rise to the surface with all the instruments. The float has a line attached to it that is also attached to the ballast on the seafloor so that everything can be recovered. In some instances a dual release arrangement is also used within the TRBM.
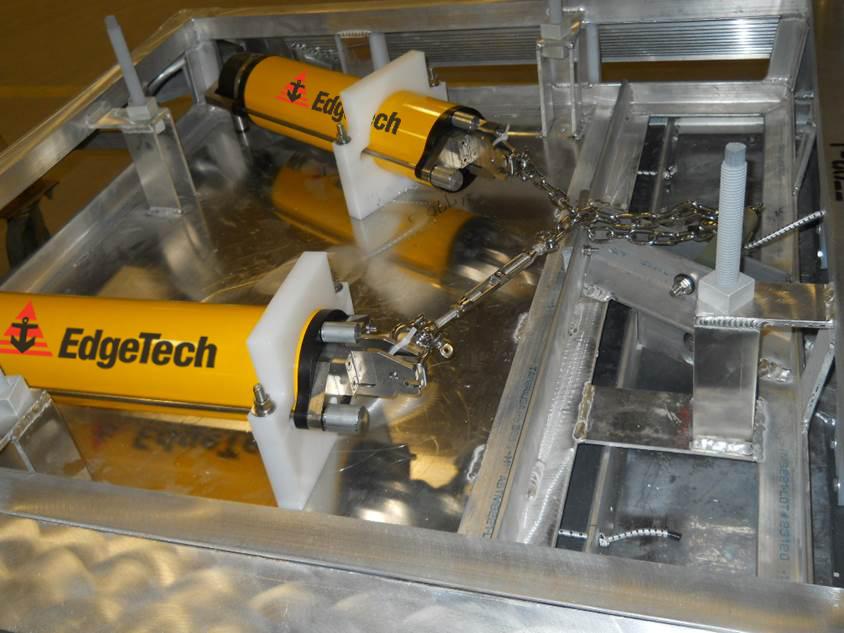
Dual Acoustic Release setup in a DeepWater Buoyancy Trawl-Resistant Bottom Mount (TRBM).
No matter what application you have, choosing the correct release is an important decision. If you are not sure what release to use for your application I am always available to help.
Choose wisely.
Rob Morris
About EdgeTech
EdgeTech Marine develops and produces a variety of standard and specialized marine products and systems including acoustic releases and USBL systems, side scan sonars, sub-bottom profilers, bathymetry systems.
Contact us at www.edgetech.com
EdgeTech Video
About DeepWater Buoyancy, Inc.
DeepWater Buoyancy creates subsea buoyancy products for leading companies in the oceanographic, seismic, survey, military and offshore oil & gas markets. Customers have relied on our products for over thirty-five years, from the ocean surface to depths exceeding six thousand meters.
Contact us at www.DeepWaterBuoyancy.com
Save
Save
Aug 30, 2016
DeepWater Buoyancy, Inc. announced today that it has added a new buoyancy product for subsea installation applications. The MiniMod™ small modular buoy is a buoyancy system that allows the end user to quickly and easily vary the amount of buoyancy for different projects.
Our current modular buoys are the most versatile approach to buoyancy for offshore applications. They are offered in a variety of standard sizes with buoyancy as great as 2 metric tons and depth ratings to 6000 meters. For installation of pipeline sleds, jumpers, or suspended moorings, this multi-purpose product offers a straightforward way to meet buoyancy requirements.
Our MiniMod™ small modular buoys are designed for lighter applications. Still rated to depths as great as 6000 meters, the standard 7-module buoy can provide up to 325 kg of buoyancy. Made from high-strength DeepTec™ solid syntactic foam that is finished with an abrasion-resistant, polyurethane elastomer coating, these buoys can stand up to rough handling on-deck and in the water.
The syntactic foam modules are held together and handled by use of synthetic straps, as opposed to metal hardware. These straps have numerous benefits including corrosion resistance, ease of handling, and no loss of buoyancy. Modules interlock for added strength and can easily be added or removed for your application.
With rugged construction and the world’s most reliable, field-proven syntactic foams, these truly modular buoys provide offshore users with years of trouble-free service.
Download a datasheet HERE
See all our product types HERE
About DeepWater Buoyancy, Inc.
DeepWater Buoyancy creates subsea buoyancy products for leading companies in the oceanographic, seismic, survey, military and offshore oil & gas markets. Customers have relied on our products for over thirty-five years, from the ocean surface to depths exceeding six thousand meters.
For further sales information: Dan Cote, Sales Manager | sales@deepwb.com | +1 207 502 1400
For further company information: David A. Capotosto | davidcap@deepwb.com | +1 207 468 8545